The Paint Protection Film Manufacturing Process in Factory
The manufacturing process of Paint Protection Film (PPF) is a complex and highly specialized procedure that begins with the careful selection of high-quality polyurethane resins (TPU/TPH), which are essential to ensure flexibility, strength and resistance to environmental factors. The raw materials are precisely extruded into a film and then coated with protective coatings and lamination processes that enhance its durability or UV resistance. Paint Protection Film requires stringent standards for production facilities, environmental conditions, and workforce expertise. Globally, only a limited number of PPF manufacturers possess complete production capabilities. For example, ELOV PPF, one of the leading manufacturers from China, has invested in a factory of more than 90,000 square meters, including a dust-free workshop, 8 automated production lines, and advanced laboratories.
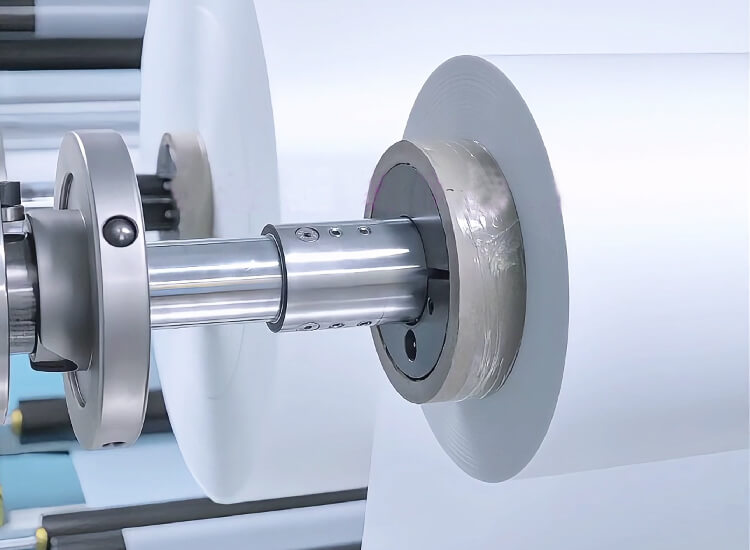
What Is Paint Protection Film and What Are the Main Types?
Paint Protection Film (PPF) is a transparent or semi-transparent polyurethane film designed to protect painted vehicle surfaces from scratches, dirt, UV rays, and other environmental factors. As consumer awareness of vehicle care increases, the demand for PPF has grown significantly. PPF is available in several varieties, including clear, matte, and colored films, making it suitable for protecting new cars, restoring used vehicles, and customizing high-end cars.
Three Main Types of Paint Protection Film On the Market Now
Clear PPF(Clear Bra), Matte PPF, Color PPF
Main Benefits of Paint Protection Film for Cars
Automotive Surface Protection: Prevents scratches and stone chips from damaging the paint.
Maintaining Vehicle Aesthetics: Helps retain the original color and finish of the paint over time.
Value-Added Services: Additional value for high-end models, enhancing customer satisfaction and appeal.
What Is Paint Protection Film?
Paint Protection Film (PPF) Manufacturing Process
The production of automotive Paint Protection Film (PPF) involves a meticulous process that demands top-notch equipment. Our dust-free workshops, automated machinery, and rigorous testing ensure high quality. After over ten manufacturing steps, including raw material blending, extrusion, coating, and quality control, the PPF is ready for shipping.
Step1. Raw Plastic Pellets Preparation
The first step is selecting appropriate plastic pellets, typically based on thermoplastic polyurethane (TPU) or thermoplastic polyolefin (TPO). These pellets are the base material for PPF and are mixed with functional additives like UV inhibitors and anti-aging agents to give the film its required physical and chemical properties.
Step2. TPU Polymer Synthesis
Polymerization: The plastic pellets undergo a polymerization reaction to produce TPU polymers with specific elasticity, scratch resistance, and transparency. The temperature, pressure, and reaction time must be precisely controlled to ensure uniformity and material stability.
Step3. TPU Raw Material Blending
Formulation Adjustment: The synthesized TPU is blended with various additives (like anti-yellowing agents, stabilizers, and plasticizers) to improve the film’s aging resistance, flexibility, and durability. The formulation is fine-tuned to meet specific application needs.
Step4 .Film Stretching and Surface Treatment
Melt Extrusion Process: The blended TPU raw material is heated to a specific temperature and extruded through an extrusion machine to form a thin film. This process controls the film’s thickness, smoothness, and clarity, ensuring a high-quality base film is produced.
Cooling and Shaping: The extruded TPU film is rapidly cooled using cooling rollers, which helps to shape the film and ensures a smooth surface.
Step5. Coating Application
Multi-layer Coating: The film undergoes multiple coating applications, typically including:
Anti-stain Coating: Provides the film with resistance to dirt and makes cleaning easier.
UV Protection Layer: Enhances the film’s ability to resist UV rays, preventing aging and discoloration.
Self-healing Coating: High-performance polymers enable the film to self-heal minor scratches when exposed to heat.
Curing Process: After the coating application, the film passes through curing ovens to ensure uniformity and adhesion of the coatings.
Step6. Quality Control & Inspection
Online Monitoring: During production, optical inspection equipment and thickness gauges are used for real-time monitoring to ensure uniform film thickness and surface quality.
Performance Testing: The film undergoes tests for tensile strength, clarity, scratch resistance, self-healing capability, and UV resistance to ensure it meets product specifications and customer requirements.
Laboratory Testing: Additional tests like weather resistance, aging, and chemical resistance are conducted to verify the film’s long-term stability in different environments.
Step7. Slitting and Rewinding
Slitting: Large rolls of finished film are slit into smaller rolls according to customer specifications, typically cut into different widths and lengths for easier application.
Rewinding: Automated equipment rewinds the film into uniform rolls, ensuring even tension to prevent deformation or damage during storage and transportation.
Step8. Packaging & Labeling
Protective Packaging: Each roll of film is wrapped with protective material to prevent scratches, contamination, or damage during shipping. Protective caps are often placed on both ends to safeguard the edges of the film.
Labeling: Each roll is labeled with specifications, batch numbers, production dates, and other relevant information to facilitate customer tracking and warehouse management.
Step9. Storage & Logistics
Warehouse Management: The finished products are stored in a dust-free, temperature- and humidity-controlled warehouse to prevent environmental damage. An automated inventory system is used to ensure accurate stock information.
Shipping & Delivery: Orders are processed and shipped according to customer requirements. Reliable and fast shipping methods are selected to ensure the products arrive undamaged.
Step10. Customer Delivery & After-sales Support
Product Delivery: Fast delivery is arranged to ensure products are shipped on time as per customer orders.
After-sales Service: Customers are provided with installation guidance, after-sales consultation, and support to ensure the best possible experience with the product.

Three Main Basic Facilities of PPF Production
Many factors affect the production of automotive PPF, but among the many factors, the following three are the prerequisites for the production of paint protection film:
Clean Room Environment: A dust-free production area prevents contaminants from compromising the film’s integrity. This is particularly important since even tiny particles can affect adhesion and clarity.
Temperature and Humidity Control: Maintaining optimal temperature and humidity levels is essential for the stability of raw materials and the finished product. Fluctuations can lead to defects in the film.
Large-Scale Production Lines: The facility should have automated production lines capable of high-volume output to meet market demand efficiently. This includes advanced machinery that can handle the intricacies of film production.
Equipment For PPF Production
There are more than one hundred types of equipment for PPF production. Here are the 20 main pieces of equipment.
Mixing Machine |
Extrusion Machine | Coating Machine | Die manchine |
Rotary Coater | Thermal Curing Oven | UV Curing Machine | Cooling Rollers |
Pulling Machine | Labeling Machine | Slitting Machine | Automatic Cutting Machine |
Tensile Testing Machine | Winding Machine | Optical Inspection Machine | Anti-Static Equipment |
UV Resistance Tester | Yellowing Resistance Tester | Automatic Packaging Machine | Labeling Machine |
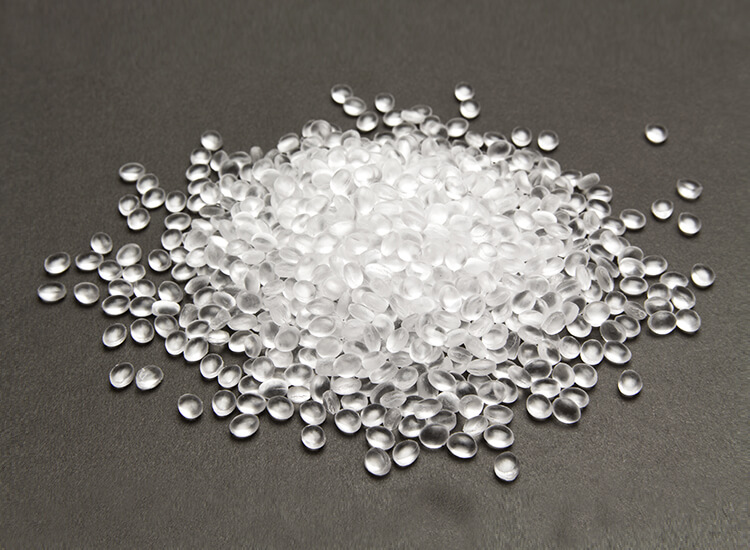
Paint Protection Film (PPF) Materials
The popular Paint Protection Film (PPF) on the market typically consists of a 5-layer design: surface protection film, self-repairing coating, TPU/TPH substrate, thermal adhesive layer, and release film. Beyond these layers, several raw materials like antioxidants, plasticizers, stabilizers, and solvents, contribute to its performance. Here are 20 essential raw materials for producing automotive paint protection film.
5 PPF Main Manufacturing Materials
Protection Film(PET): Suppliers – DuPont, Toray Industries
Self-repairing Coating: Suppliers – Mitsubishi Chemical, Cashew, BASF
TPU Substrate: Suppliers – Covestro, BASF, Wanhua Chemical
Thermal Adhesive Layer: Suppliers – Ashland, 3M, Henkel, Lubrizol
Release Film: Suppliers – Lintec, Intertape Polymer Group
Other PPF Manufacturing Material
Plasticizers
Anti-yellowing agents
Stabilizers
Antioxidants
Anti-soiling coating materials
UV-resistant coating materials
UV additives
Pigments
Coating solvents
Curing agents
Protective films
End caps
Paper or plastic cores
Label materials
Static eliminators
Lubricants
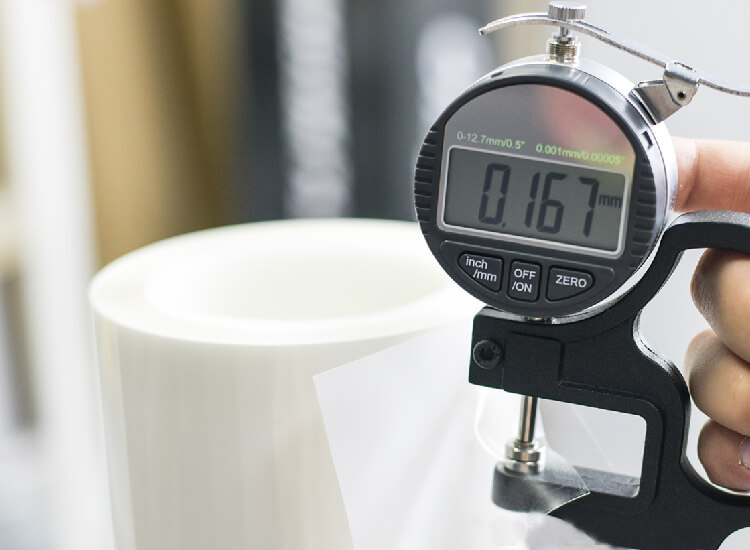
Quality Control and Tests
The quality control of PPF production is generally achieved through in-process quality control (IPQC) and a series of tests (QC).
Online Quality Control
PPFs with appearance defects are typically identified and removed during production using automated visual inspection.
For instance, ELOV PPF employs an advanced 80-million-pixel inspection system, which offers six times the resolution of human vision, allowing it to detect even the slightest defects.
Tests: Raw material, TPU, Coating Material, PSA, Release Film., etc
PPFs with appearance defects are typically identified and removed during production using automated visual inspection.
For instance, ELOV PPF employs an advanced 80-million-pixel inspection system, which offers six times the resolution of human vision, allowing it to detect even the slightest defects.
Raw material testing
Ensure that all incoming materials meet the specified technical requirements and effectively prevent defects in the final product. It mainly includes 5 major categories of testing:
TPU (thermoplastic polyurethane) Testing
1. Melt Flow Index, MFI
2. Tensile Strength
3. Elongation at Break
4. Hardness, Shore A
5. Abrasion Resistance
6 . Weather Resistance
Coating Material (self-repairing, anti-fouling, etc.) Testing
1. Adhesion Test
2. Self-healing Performance
3. Chemical Resistance
4. UV Resistance
5 . Yellowing Resistance
6. Surface Hardness Test
Pressure Sensitive Adhesive (PSA) Testing
1. Peel Strength Test
2. Tack Test
3. Shear Adhesion Test
4. Aging Resistance Test
Release Film Testing
1. Release Force Test
2. Surface Smoothness Test
3. Thickness Uniformity Test
4. Aging Resistance Test
Additive Testing Items
1. Dispersibility Test
2. Oxidation Resistance Test
3. UV Stabilizer Efficiency Test
Car Paint Protection Film Finished Product Testing(Laboratory Tests)
Involves a comprehensive evaluation of the film’s properties. 16 Key tests include:
1. Scratch Resistance Test
2. Abrasion Resistance Test
3. Impact Resistance Test
4. UV Resistance Test
5. Corrosion Resistance Test
6. Water Spot Resistance Test
7. Yellowing Resistance Test
8. Tensile Strength Test
9. Adhesion Strength Test
10. Chemical Resistance Test
11. Gloss Retention Test
12. Thermal Aging Test
13. Low Temperature Flexibility Test
14. Stain Resistance Test
15. Self-healing Test
16. Optical Clarity Test
Recommend: Top 10 Global Paint Protection Film (PPF) Manufacturers
Here are ten renowned manufacturers in the PPF industry, known for their high-quality products and technological advancements:
3M
XPEL
SunTek
Llumar
V-Kool
Hüper Optik
Solar Gard
Johnson Window Films
ASWF
ELOV PPF
Summary and Suggestions
The manufacturing process of Paint Protection Film (PPF) is intricate and requires a combination of high-quality raw materials, advanced production facilities, and stringent quality control measures. Manufacturing can only meet consumers’ growing demand for vehicle protection solutions by giving automotive PPF more practical performance through continuous innovation and technological progress.
ELVO Offers Fast Paint Protection Film OEM |
25 Days |
From Ideas To Mass Production |
Start OEM For Your Brand Now! |